Aircel AEHD Series / Externally Heated Regenerative Desiccant Dryer
Regenerative compressed air dryers use desiccant to adsorb water vapor from the compressed airstream. In the twin tower design one tower dries the air from the compressor while the desiccant in the other tower is being regenerated to provide continuous operation. These dryers are typically referred to as “heatless” or “heated”. Heatless dryers do not use any source of heat for regeneration other than the heat given off during the drying phase. This is known as the “Heat of Adsorption”. Heated dryers, on the other hand, utilize an external heat source for regeneration and require little or no process air.
The Aircel AEHD Series Dryers (150 - 3,000 scfm) utilize process air for regeneration of the desiccant bed similar to the heatless designs. However, this expanded process air is heated prior to entering the off-line bed, significantly reducing the required consumption and the cost of operation. Additionally process air is consumed during depressurization of the offline desiccant tower. In total these functions amount to an average process air use of 7% of the rated capacity of the dryer.
FEATURES
- Removable, stainless steel desiccant bed support screens
- Tower pressure gauges
- ASME code desiccant towers (6” vessels and larger)
- High temperature outlet check valves
- Fail-safe design
- 1-1/2” thick fiberglass insulation
- Highly reliable programmable logic control (PLC)
- Energy saving venturi option available on request

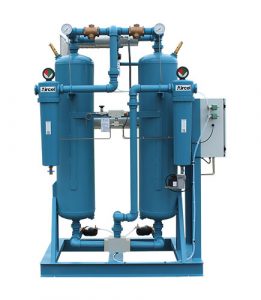
Filtering and drying incoming air. Hot, saturated compressed air is filtered as it passes through our 0.01 micron high-efficiency coalescing prefilter (F1, recommended option) before entering the dryer. Compressed air continues through the inlet valve (V1), is dried in the desiccant tower (T1), and exits through an outlet valve (V5) and final particulate filter (F2, recommended option), while the other desiccant tower (T2) is being regenerated.
Desiccant regenerated in T2. A portion of the dried air is diverted through purge valve (P3) at near atmospheric pressure and heated by the electric heater (or optional steam heater) to 400°F before passing through regeneration valve (V4) and into the regeneration tower (T2). The heated air removes moisture vapor from the desiccant surface.
Dryer operation is performed automatically by a programmable logic controller (PLC). The standard drying and regeneration time cycle is 8 hours. While one tower is drying incoming compressed air for 4 hours, the other tower is regenerating for 3 hours (heating time), then cooling for 50 minutes, and finally repressurizing to the line pressure for 10 minutes Filtering and drying incoming air. before switching over to the other tower. Switching from one tower to the other is performed only when both desiccant towers are at line pressure to prevent line surge and to minimize desiccant abrasion.
Model | Capacity1 (scfm) | Connection (inches FNPT/ANSi) |
Heater kW | Full Load Amps | Voltage (Standard) | Dimensions (inches) | Pressure max. (psig) | Weight (lbs) | Desiccant Both Vessels (lbs) | ||
---|---|---|---|---|---|---|---|---|---|---|---|
Height | Width | Depth | |||||||||
AEHD-150 | 150 | 1 | 2.5 | 3.2 | 460V/60 Hz/3Ph | 75 | 45 | 30 | 150 | 810 | 200 |
AEHD-250 | 250 | 1-1/2 | 4.5 | 6.2 | 460V/60 Hz/3Ph | 75 | 50 | 35 | 150 | 1200 | 400 |
AEHD-350 | 350 | 2 | 6 | 8.1 | 460V/60 Hz/3Ph | 75 | 54 | 35 | 150 | 1600 | 500 |
AEHD-500 | 500 | 2 | 9 | 11.8 | 460V/60 Hz/3Ph | 83 | 60 | 39 | 150 | 2000 | 700 |
AEHD-750 | 750 | 3 FLG | 12 | 15.6 | 460V/60 Hz/3Ph | 89 | 75 | 44 | 150 | 2600 | 960 |
AEHD-1000 | 1000 | 3 FLG | 15 | 19.3 | 460V/60 Hz/3Ph | 98 | 88 | 54 | 150 | 3500 | 1400 |
AEHD-1200 | 1200 | 3 FLG | 20 | 25.6 | 460V/60 Hz/3Ph | 109 | 96 | 60 | 150 | 3900 | 1800 |
AEHD-1500 | 1500 | 4 FLG | 24 | 30.6 | 460V/60 Hz/3Ph | 109 | 102 | 69 | 150 | 4500 | 2100 |
AEHD-2000 | 2000 | 4 FLG | 30 | 38.2 | 460V/60 Hz/3Ph | 115 | 120 | 69 | 150 | 5800 | 2800 |
AEHD-2500 | 2500 | 4 FLG | 36 | 45.7 | 460V/60 Hz/3Ph | 115 | 130 | 73 | 150 | 6600 | 3600 |
AEHD-3000 | 3000 | 6 FLG | 45 | 57.00 | 460V/60 Hz/3Ph | 120 | 140 | 77 | 150 | 7500 | 4200 |
Fill the form below for our sales expert to contact you to discuss about your requirement. We respect your privacy and will not share your personal information with others.