September 16, 2020
Tips to create and maintain an energy efficient compressed air system.
Air compressors support many industries, from small auto shops powered by reciprocating compressors to large-scale vertically integrated textile units powered by high volume centrifugal compressors. Air compressor technology is simple. Powered pistons, screws or impellers compress a volume of atmospheric air to a required pressure for an application. The design and use of compressed air systems have evolved to suit varying industry needs. Over time, manufacturers have invested in technology to overcome air compressor inefficiencies and to simplify the user experience. However, compressed air remains a major utility expense
Image 1 shows the typical life cycle cost breakdown of a compressor. Power consumption accounts for nearly 88 percent of a compressor’s 10-year life span cost. Up to 50 percent of air is wasted, resulting in thousands of dollars lost in energy, according to the United States Department of Energy (DOE). There are many factors that contribute to an inefficient operation.
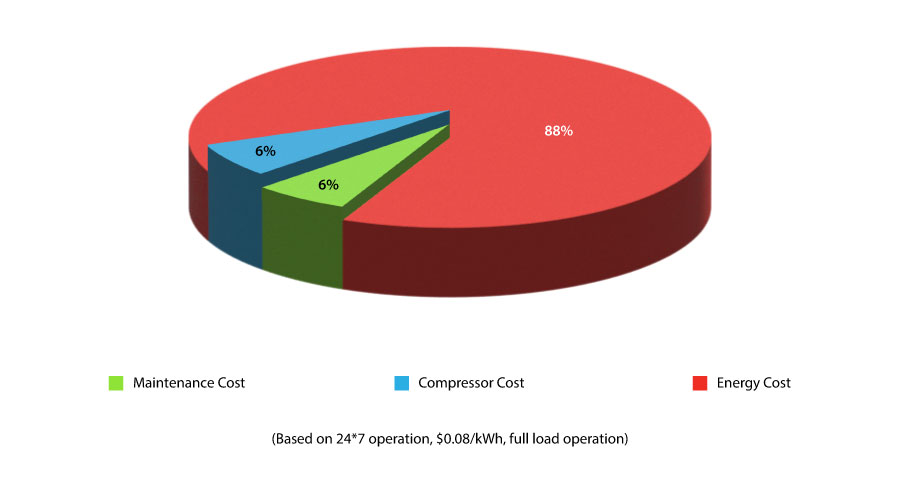
IMAGE 1: Compressor life cycle cost breakdown (Images courtesy of ELGi North America)
Here are three main points to evaluate to transform utility cost into an energy saving opportunity.
1. Compressor Size
Bigger is not better when it comes to air compressors. A rotary screw compressor is most efficient when running in a 100 percent loaded condition. (Loaded, means the compressor is producing air; while unloaded means the compressor remains idle.) A compressor will continuously load when its air production capacity matches the air requirement. For example, if a compressor produces 500 cubic feet per minute (CFM) but the air requirement is only 300 CFM, then the compressor will be in unload condition for a significant portion of the time. Screw compressors are inefficient in the unload condition and, thus, a larger compressor will use more energy and consumables than a right-sized compressor for a given air requirement.
As a general rule of thumb, a compressor that is only running at 50 percent capacity will consume 20 percent or more power than a compressor that is running at or close to full capacity.
2. Fluctuating Air Demands
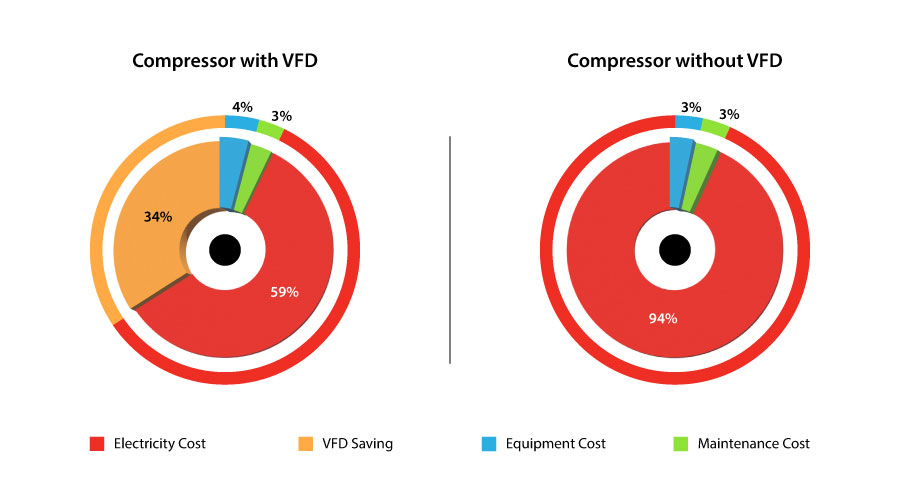
IMAGE 2: Benefits of a VFD
Determining the right size can be sufficient to improve energy efficiency, but what about those customers who have varying demand patterns during the day or those customers who anticipate an increase in manufacturing capacity requiring more air? Variable frequency drives (VFDs) provide solutions to both situations.
A VFD works by reducing the compressor motor’s speed to lower fl ow to match the actual air demand of the customer.
By reducing the motor’s speed, the compressor consumes less energy than a fixed speed compressor versus inlet modulation control or load/no load (at 3 gallons per CFM storage). Image 2 illustrates the power savings with a VFD.
3. Air Distribution System
When looking to improve energy efficiency, customers have to look further than the air compressor and evaluate the compressed air system as a whole. The biggest area for improvement could be the facility’s distribution system—how the compressed air is transported and used in the end application. Both the design of the distribution and material used for piping affect energy efficiency.
When designing a compressed air piping system, the shorter the distance from the compressor to the application, the better.
Minimizing bends en route to the application reduces pressure drops and improves the efficiency of the system.
Image 3 compares an inefficient line design versus an efficient design. Many vendors may not be able to provide sweeping elbows that minimize pressure drop, so for practical purposes, if a vendor can only provide 90 degrees of piping, consider upsizing the pipe diameter by 1 inch to minimize pressure drops.
Choosing the material for the distribution system is as important. Plastic, aluminum and steel are the most common materials for compressed air piping. While steel is more accessible than aluminum, aluminum offers lower weight and corrosion resistance. Compressed air contains trace amounts of oil and water, which can cause line corrosion and, in turn, results in pressure drops and affects effi ciency.

IMAGE 3: Best practices for compressed air design
In addition, compressed air lines are dynamic in that they are constantly vibrating owing to the passage of compressed air. Over time, these movements weaken joints and can result in leaks. Leaks found in a facility’s air compressor system can waste up to 25 percent of compressed air costing, thousands of dollars in electricity per year
Air Audits Find Inefficiencies
Air audits determine the actual air demand and evaluate the efficiency of use of compressed air in an operation. Air audits can determine the appropriate size needed, evaluate the need for a VFD, identify inefficiencies in piping design and ultimately optimize usage.
Compressor manufacturers and compressed air experts are capable of conducting air audits. An air audit expert will use data loggers, flow meters and leak detection devices to evaluate an operation’s air usage.
Typically, the auditor will spend days gathering data to fully understand the varying demand conditions and the nature of use. Following the analysis, they will issue a report with a summary of the potential savings along with recommended changes and associated costs.
Following the recommendations requires an initial investment and continuous maintenance, but payback is usually seen in a short time. Consult with a compressed air specialist to see what steps can be taken to pursue energy efficiency. By running an energy efficient operation, users work toward saving money and creating a more sustainable future.
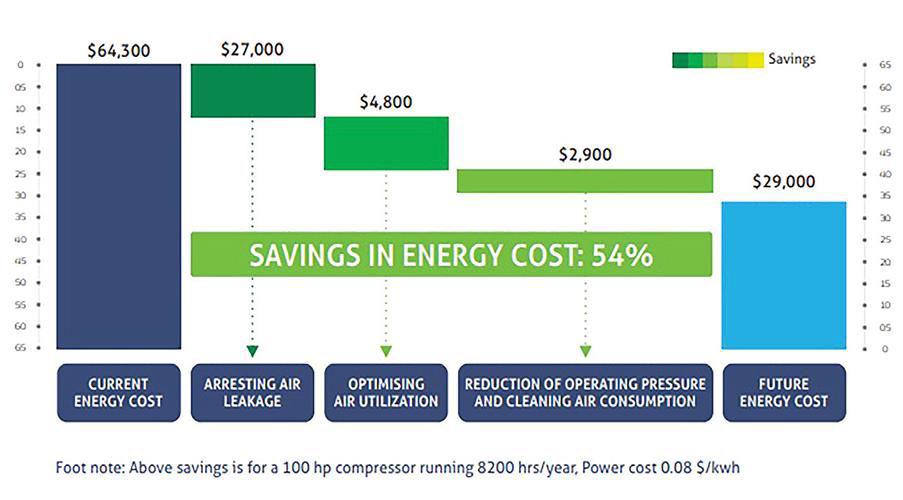